The landscape of Additive Manufacturing is continually evolving, with a growing roster of materials becoming compatible with 3D printing. In the realm of metal 3D printing, ongoing advancements lead to the optimization of novel metals and alloys. This progress enables the creation of components boasting traits like superior strength and resistance to corrosion, to name just a few.
Consider steel, a frequently employed metal with a rich variety of types, each endowed with specific strengths and weaknesses. Tool steel is one such variant, used extensively in tools due to its remarkable hardness and ability to maintain its shape. However, its susceptibility to corrosion, owing to low chromium levels, is a drawback.
Stainless steel bridges this gap, presenting a range of alloys fortified with varying levels of chromium to guard against corrosion and damage. Most stainless steels fall within the 300 or 400 series. The 400 series, with its higher carbon content, offers strength and wear-resistance but lacks nickel, increasing its susceptibility to corrosion.
Among the 300 series alloys, 316 stainless steel stands out. This alloy, infused with molybdenum, boasts heightened resistance to corrosion, making it a go-to material for outdoor applications. Its variant, 316L stainless steel, contains less carbon, which imparts even greater corrosion resistance… hence the “L” for “low carbon.”
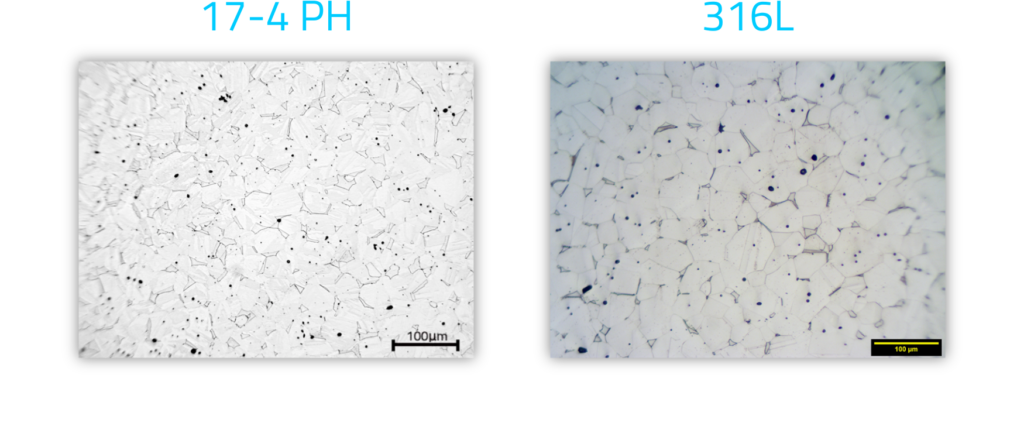
3DEO’s martensitic 17-4 PH grain structure compared to 3DEO’s austenitic 316L grain structure
When we explore the crystalline structure of steel, we find three key types: ferritic, martensitic, and austenitic. Among these, austenitic steel possesses the greatest strength. The 316L stainless steel is an austenitic variant, meaning its primary crystalline structure is face-centered cubic, achieved through high-temperature heating and subsequent rapid cooling or quenching.
This austenitic steel, 316L, is a non-magnetic material that excels in performance at room temperature and moderately high temperatures. Its low carbon content significantly reduces the risk of carbon precipitation, making it an appealing option for welding applications.
While 304 stainless steel is commonly used in consumer and industrial applications due to its corrosion resistance – thanks to chromium and nickel alloys – and requires no annealing post-welding, it falls short of the superior corrosion resistance offered by 316L stainless steel, which benefits from higher molybdenum content.
Indeed, in terms of corrosion resistance, 316L stainless steel outshines many other metals. It performs admirably in marine environments, resisting damage from water and salt. Its resilience in harsh environments makes it highly attractive to manufacturers seeking to leverage 3D printing for industrial or automotive applications.
Moreover, 316L stainless steel exhibits exceptional ductility, which means it can be deformed without breaking. It is both stronger and more malleable than 17-4 PH, another common type of stainless steel. Due to its biocompatibility, it is also a preferred choice for medical devices and surgical instruments.
This versatile material finds use in numerous applications – from impellers and pumps to laboratory equipment, engine parts, food processing equipment, jewelry, kitchen appliances, and even marine, chemical, and petrochemical processing. As Additive Manufacturing continues to pervade more industries, 316L stainless steel is becoming an increasingly attractive option for 3D printing.
At 3DEO, we have embraced the dynamic capabilities of 316L stainless steel, harnessing its superior characteristics in our innovative manufacturing processes. Our team’s proficiency in Additive Manufacturing combined with our expertise in utilizing materials like 316L stainless steel allows us to deliver outstanding products and solutions to our clients. We understand the transformative impact that 3D printed 316L stainless steel can have on diverse sectors such as aerospace, healthcare, automotive, and more. We invite you to discover the potential of 316L stainless steel and how we can help you leverage its benefits.
Connect with our team today, and let’s explore how 3DEO’s commitment to advanced manufacturing can unlock new possibilities for your business.